Introduction: DIY Adirondack Chair
Are these the most comfortable wooden chair that you'll ever sit in? Of coarse they are, although I may be a little biased. It's my Adirondack Chair build, but done entirely with just 6 handheld power tools (not table saw, bandsaw, etc.)! This time I also added in a brand new pull out footrest that collapses inside the chair so you don't even know it's there, plus it has multiple positions AND it's curved so that makes it super comfortable. I'm surprised I'm even typing this up right now because that means I've gotten out of the chair. The chair is made from clear grade western red cedar lumber, fastened together with stainless steel screws and carriage bolts, and finished with TotalBoat epoxys and boat varnish.
But I know what you clicked for, here's the chair in action!
If you're interested, I also have plans available for the chair:
Chair plans - http://bit.ly/2nh4mra
Footrest plans - http://bit.ly/2kayqEu
Step 1: Materials & Tools
Notable Materials & Tools used on this build:
Materials
- Adirondack chair physical template (optional) http://bit.ly/2lDLfHI
- (30 Linear Feet) 5/4x8 lumber (1"x7-1/4" finished dimensions) + (9 linear feet for footrest)
- (68) 2" stainless steel screws + (32 for footrest) https://amzn.to/314Bl1L
- (6) 2-1/2" long 1/4" carriage bolt, nut, washer + (2 for footrest) https://amzn.to/316olsm
- Epoxy resin http://bit.ly/2koIb25
- Penetrating epoxy http://bit.ly/2lE2fgY
- Exterior varnish finish http://bit.ly/2lBcra1
Tools
- Hearing protection - http://bit.ly/2kyghk5
- Respirator (use code "Jackman" for 5% off!) - https://bit.ly/2zOvwwn
- Circular saw http://amzn.to/2pindD0
- Jig saw https://amzn.to/2Hs9rVk
- Belt sander http://amzn.to/2oS8zyE
- Speed square http://amzn.to/2C7Vqaa
- Palm router https://amzn.to/2UL6rsL
- 3/8" quarter round router bit https://amzn.to/2KVJwrt
- Drill & Driver http://amzn.to/2wy5wSZ
- Countersink/screw bit http://amzn.to/2jg0S0Z
- Random orbit sander https://amzn.to/2MZBVKR
- Jorgensen F style clamps https://amzn.to/2ZJf1OB
- HVLP sprayer https://www.rockler.com/rockler-hvlp-finishing-spr...
Step 2: Layout
My chair is made from 5/4 x 8 clear vertical grain western red cedar. The boards come rough sawn, so I plane them down to a finished 1" thickness, any good lumber supplier will do the same for you if you don't have a thickness planer. I have plywood made for the chair, so I use those to layout and trace my pieces on the boards. The shapes next together, so I take advantage of that while bouncing around any imperfections in the lumber (which is super minimal with this type of lumber). It took me roughly 26' total of cedar for this chair and 9' for the footrest.
Step 3: Rough Sizing
The boards are rough cut down to length with my circular saw to make them more manageable. I make sure not to cut to the line at this point, leaving me some room to refine the cuts later. If I can't cut straight across the board, I tag in my jigsaw to assist in breaking the boards down (me and my jigsaw are tag team champs, baby!)
Now that the boards are more manageable, I cut out the actual pieces. Like me, these parts have a lot of curves, so I use my jigsaw to do this, leaving about 1/16" outside of the line to sand down later.
Step 4: Ripping
Any straight lines are cut with a circular saw. With a steady hand you can make surprisingly straight rip cuts with a circular saw. All of the seat slats and back slats are cut down to width using this technique. It's all in the hips, it's all in the hips Happy! For real though, one steady motion and it'll look like you cut it on the table saw. Cutting to final length will happy later, after sanding.
An alternative technique for ripping boards down to width is available, but I won't discuss the details of that here. This technique requires a professional woodshop, and a sponsored YouTube channel, which just isn't in the spirit of "DIY".
Step 5: Sanding Edges
Next, I can sand the pieces all down to the line that I left on there before when cutting them out. A belt sander is all you really need, this will sand the flat edges easily, plus with a little dexterity the front roller acts as a spindle sander and can sand down inside curves. This technique might actually be more efficient then using benchtop tools because I can sand multiple matching pieces at the same time.
Step 6: Cutting Pieces to Length
With the edges sanded down to the line, I now have a perfect reference surface to cut all of the square ended pieces down to length. I use my speed square as a guide and clamp it up on the edge of the piece with my hand and use that with my circular saw to cut right on the line.
My lonely miter saw was watching this whole process. The things I do for you people.... yeah, you know what I mean!! "you people"!
Step 7: Round-Over
Last step of shaping the pieces is rounding over the corners on the pieces. The top and bottom of the arms are rounded over, the top of the back slats, the top of the seat slats, etc. I use a 3/8" round over bit in my palm router and mount the router in my bench vise so that it acts as a router table. This is more for the smaller pieces though, the router can be used like normal for larger pieces like the arms and legs.
Step 8: Pre-Drilling
Now certain holes are predrilled in the pieces before assembly, using my templates to determine the location. The holes for carriage bolts that attach the legs are drilled out 9/32" to give enough room for the 1/4" bolts to have a little wiggle room.
The smaller holes are drilled out 7/32" to give just enough room for the stainless screws to pass-through, which is what holds the majority of the chair together. The back slats are drilled out along the bottom and the middle slat is drilled at the top to get me started with the assembly process which you'll see more of later.
Step 9: Sanding
Prior to assembly, I just sand every piece down to 220 grit with a random orbital sander. I also soften all of the hard edges at this point by just passing over them by hand with 220 grit sandpaper.
Step 10: Assembly - Legs
And finally, the best part of the build can happen, the assembly. There's just so much build up with preparing the pieces of the chair and this climaxes with the assembly of the chair which is such a fast part of the process and just leaves you disappointed that it was completed so quickly. Anyway, assembly starts with the front legs of the chair, the arm supports are centered on the top side of the leg and held in place with 3 screws.
The front legs can then be attached to the main bag leg with 3 carriage bolts, washers, and nuts to create the leg sub-assemblies. For now these are just screwed finger tight, they will be bolted down at the final step of the assembly of the chair when the chair is checked for flat/square.
Step 11: Assembly - Back
The legs are set aside, and the back sub-assembly is next. The back slats are all centered on the bottom back support and the center slat is screwed into place first, then checked for square and adjusted as necessary (but of coarse with my eyes, no adjustment is ever necessary). The rest of the back slats are then screwed in place on either side.
Next, the top back support is added to the assembly by centering all of the back slats on it and then pre-drilling and screwing the center back slat in place. Now I measure both the left and right side to make sure the measurements are the same, this means that the upper and lower back supports are parallel with one another.
The sub-assembly is completed by rotating the outer most back slats to the edge and screwing them in place, then the other 2 slats between that and the center slat are spread out evenly and screwed in place. The beauty with the design of this chair is that dimensions just need to be close enough to look good, if your eye can't see the difference, you're close enough. But I won't be telling that to too many people because I might lose what little respect people have left for me.
Step 12: Assembly - Combining Back & Legs
Now the back and leg sub-assemblies can be joined in holy matrimony. As we say, it's back and leg, not back and..... keg? Honestly I don't have a good punchline for that joke, but I want credit for it regardless. The back is attached where the lower back support fits into the notch in the main back leg. Each side is screwed in place with a single screw, then the front of the chair is measured to check for parallel, and the a 2nd screw can be added to each side.
Step 13: Assembly - Seat Slats
The seat slat installation process starts by installing the back most slat tight against the back slat of the chair. The front most slat (the one that isn't the extra wide slat) is installed tight against the front edge of the front legs. These slats are centered left to right and then attached with a screw on each end.
2 of the seat slats are positioned between the front legs, so they need to be trimmed down a little bit shorter. I use my bench mounted circular saw to nibble off a little from each side. Note that this is definitely a bench mounted circular saw and not a miter saw, two completely different tools! Don't @ me.
The remainder of the seat slats are installed by evenly distributing them and screwing them in place. I find that the gap is right around 7/16" between them. I attache one side of all of the seat slats and then do the same on the other side of the chair.
Step 14: Assembly - Back Support Leg
Next, the back support legs are added by pre-drilling and screwing them in place through the upper back support.
The bottom of these is fastened in place on the back inside face of the main leg. Pro-tip, I pre-drill these at a slight angle so that the 2" long screws won't poke out the side of the chair.
Step 15: Assembly - Arms
And the last piece to be attached is the arms! The back side of the arms have a notch that fits over the back support legs and each is screwed in place with a couple of screws. Then the front of the arms receives 3 screws, 2 of them into the front leg and 1 into the arm support.
Step 16: Assembly - Footrest
Well, I have one last thing up my sleeve which was supposed to be a surprise, but you already saw it so please just act surprised to appease me. Ok? Cool. So I've made these chairs before, but the leg rest is a brand new addition which I worked the design out for off camera. The build process is the same and requires little modification to the existing chair. Plus, offers multiple positions, still has a curved surface, and collapses completely into the chair so you can't even tell it's there. Alright, alright, calm down, it's not really that exciting. But! AdD A sEt Of LeGs To ThE BaCk AnD MaKe It A tAbLe ToO!! Nope, the top surface of the table would be curved and I can't be trusted not to place spillable things on a curved table.
Step 17: Finish - Sealing Up Legs
Now it's time for finish! Applying finish to outdoor furniture is always a process, but for anything that lives outside it'll be worth it because it'll help to make it live even longer. First step for applying finish is to disassemble the chair. Really though, that's just a step for me because I only assembled the chair in order to design the footrest. Anyway, first step is to seal up the legs with epoxy resin. The end of all of the legs that touch the ground are end grain, which means that they like to suck up water. To prevent this, I flip the legs upside down and tape them off, then drench the end grain with epoxy. Once this cures I can sand the legs flat.
Step 18: Finish - Sealing With Penetrating Epoxy
2nd step is applying a coat of finish prior to assembling the chair. Every side of every piece gets coated in a 2-part penetrating epoxy, which is a super thin epoxy that soaks into the surface. This both seals up the pieces to the weather for better stability and it also hardens when it cures which helps to create a slightly harder surface on the soft cedar pieces.
Step 19: Final Assembly
Now is the time that I should have assembled the chair, but I'll go ahead and reassemble it in fast forward instead. Also, now that the final assembly is done, I can verify that the chair is flat. I do this by placing it on a flat surface to see if it wobbles at all, if it does then I twist the chair until it's flat and then at that point I can tighten the carriage bolts all the way with a socket.
Step 20: Finish - Varnish
3rd and final step for finishing the chair is varnish. Me and my sexy friend load up the hopper of my HVLP sprayer with TotalBoat Halcyon amber varnish, which is a super tough boat varnish that I'd venture will be good enough for a chair. I did some test and decided not to thin it at all because it sprayed just fine straight from the bag.
I use the sprayer to apply 4 coats of varnish to the chair, allowing them to cure between coats. Amber finish the is the only choice for cedar IMO, there's just nothing else that pulls that color out so well.
I do the spraying outside for ventilation, but I set up a tent overhead to protect the finish from the sun. This is a water-based finish so it dries fairly quickly. If I was in direct sunlight, the finish would dry too quickly so it wouldn't have enough time to level out and create a smooth surface. Ask me how I know, or don't, because you know how I know, you know?
Step 21: Finish - Varnish Final Coat
After the 4th coat cures, I go over the entire surface by hand with a 220 grit sanding sponge. This knocks down any uneven or fuzzy spots of the finish, this is especially noticeable on the corners and around the end grain where it absorbs differently.
The chair and footrest are then wiped down with a rag to remove any dust that was left behind from sanding. Now the final coat of finish can be applied. The difference between the 4th and 5th coat is always amazing and surprising with it being so buttery smooth, totally worth it (pro-tip - varnish doesn't taste like butter).
Step 22: Glamour Shots
Now all there is left to do is relax out on the Potomac River. And as well all know, the Potomac is exclusively BYOC (bring your own chair).
Thanks for checking out the build! For the full build experience and more details, checkout the full YouTube build video (linked down below). And lastly, let's talk about this legend! This man right here is my carpentry teacher from high school, the one who taught me how to build these chairs. I decided to gift the chair to him because I knew no one else would appreciate the chair more. Plus, I know he's 100% going to steal the footrest addition and make his own set of templates so he can add those to his chairs now ;)
----------------------------------------------------------------------
Thirsty for more? You can also find me in other places on the interwebs!
My Website: Essentially my entire life
YouTube: Me, in moving picture form
https://www.youtube.com/jackmanworks
Instagram: Preview my projects as they progress #nofilter
https://www.instagram.com/jackman_works
Twitter: Riveting thoughts, in very small doses
https://www.twitter.com/jackmanworks
----------------------------------------------------------------------
Note: This post contains affiliate links. Thank you for supporting what I do!
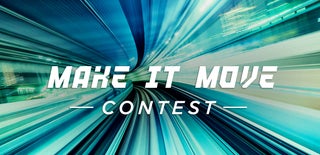
Participated in the
Make it Move